The Art of Prototool’s Machining Magnesium: Forging the Future
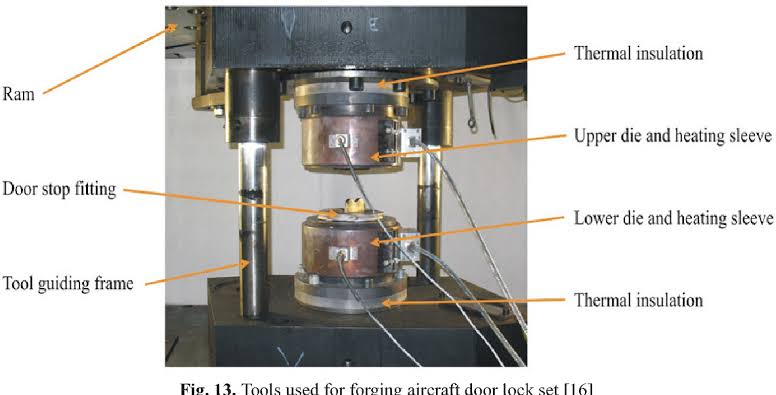
In industries ranging from aerospace to automobile, machining magnesium, a delicate and reactive metal, offers distinct challenges and possibilities. This adaptable material is well-known for its high strength-to-weight proportion, making it a tempting option for operations where less weight is crucial. However, its properties necessitate specific machining procedures and safeguards. Prototool’s machining of magnesium offers a wide range of applications. Let’s dig deep into it:
Applications of machining magnesium
Prototool’s machining magnesium is commonly used in aeroplane elements such as wings, landing gear, engine assemblies, and supporting structures. Magnesium is used in lightweight gearbox cases and engine assemblies in the car industry to optimise fuel savings.
The durable and lightweight qualities of magnesium aid healthcare equipment such as surgical tools and prosthetics. Sporting supplies, such as frames for bikes and golf club heads, use the lightweight feature of the product to improve performance.
Why should you be careful when machining magnesium?
Although it has numerous benefits, you should be careful while igniting Protolool’s magnesium for the following reasons.
Fire Risk: The combustibility of magnesium is one of the most severe issues when machining it. Because the metal ignites when it comes into the presence of oxygen, limiting the accumulation of fine magnesium flakes is critical.
Low Thermal Conductivity: Because of its thermal conductivity, the heat generated while machining tends to dissipate. It can result in tool wear and a shorter lifespan of the tool.
Tool Selection: Because magnesium is harsh and flammable, choosing the correct cutting equipment is crucial. Equipment that can withstand high temperatures while generating little heat is essential.
Surface Finish: Given that magnesium tends to develop chips, obtaining a finish on a surface that is smooth can be difficult.
Magnesium Machining Techniques
When using Prototool’s parts machining, many essential approaches are used to address these challenges:
Controlled atmosphere: Magnesium machining is frequently performed in a controlled atmosphere with low oxygen levels. It can be accomplished by creating a protected atmosphere with inert gases such as argon.
Cutting Velocity and Feed Rate: Lowering the velocity of cutting and the rate of feed during the process could reduce heat generation. To avoid tool wear, it’s critical to achieve a balance.
Tool Coatings: When machining, using tools for cutting with suitable coatings, such as carbon or carbide, can improve durability.
Lubrication: To mitigate heat and friction, adequate lubrication is required. Because dry milling is not suggested due to the fire risk, it is usual practice to use certain coolants or grease.
Chip Control: Using efficient chip preventative measures lowers the build-up of magnesium flakes and the probability of fires.
All in all, because of its particular features, such as flammability, low heat conductive properties, and abrasiveness, Prototool’s machining magnesium calls for a sophisticated approach. Nevertheless, with the proper skills, tool picks, and safety precautions, it may serve as an excellent metal to work within a variety of applications where a reduction in weight and durability are essential.