From idea to reality: The power of prototyping in the manufacturing process
In the ever-evolving and highly competitive manufacturing world, prototyping has emerged as a critical and indispensable tool that brings unprecedented efficiency, innovation, and cost-effectiveness to the production process. This invaluable practice involves the creation of preliminary models, meticulously crafted and fine-tuned, to provide an integral preview of potential products.
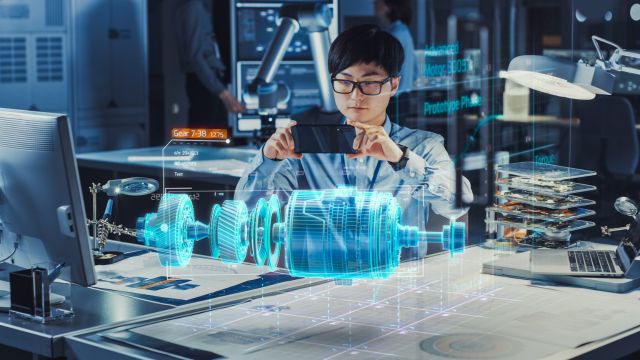
By thoroughly evaluating these prototypes, manufacturers gain unparalleled insights into their designs, allowing them to rectify flaws, refine every intricate detail, and enhance overall functionality before mass production. With prototyping as a crucial step in the manufacturing workflow, it empowers companies to optimize their production lines, minimize risks, and deliver exceptional products that exceed customer expectations.
The potency of prototyping
Prototyping is not a one-size-fits-all process; it assumes various forms and shapes depending on the product, complexity, and intended purpose. Regardless of the structure, prototyping forms a cornerstone in the manufacturing industry as it allows companies to experiment with new ideas while minimizing potential risks.
Prototypes offer an opportunity to test different materials, production techniques, and designs that would have otherwise cost companies millions in full-scale production. By providing a platform for experimentation, prototyping empowers engineers and designers to explore their creativity without fearing failure. It allows them to tweak designs until they achieve an ideal product that meets all functional and aesthetic requirements.
The power of prototyping extends beyond just experimenting with ideas; it also enables manufacturers to detect potential design flaws early in development. Through this practice, companies can eliminate costly mistakes at a much lower cost, saving them both time and resources.
Prototyping as a catalyst for innovation
Innovation is the driving force behind success in the manufacturing industry. It dictates the design of new products and services that meet evolving consumer needs. In this regard, prototyping is a powerful catalyst for innovation by allowing companies to explore new possibilities, develop groundbreaking products, and keep pace with changing market trends.
With prototyping, manufacturers can quickly create multiple variations of the same product, testing each design to determine which offers the most desirable outcome. The ability to generate rapid prototypes means that companies can respond swiftly to consumer demands, making real-time adjustments and improvements. This level of agility is paramount in a rapidly evolving market, where companies must stay ahead of the competition to remain relevant.
In addition to fostering innovation, prototyping encourages networking and collaboration between different teams and departments within a manufacturing company. Prototyping promotes seamless communication and invites diverse perspectives in the design process by providing a tangible model that all stakeholders can review and provide feedback on. It ensures that all aspects of a product are thoroughly evaluated before mass production, resulting in a superior end product.
The cost-effectiveness of prototyping
One of the most significant advantages of prototyping in manufacturing is its cost-effectiveness. Traditional methods of product development involved creating molds and dies before producing a single unit, which increased costs and extended lead times. Companies had to invest considerable time and money upfront to know if the final product would meet customer expectations.
Prototyping eliminates these extra expenses by allowing companies to identify and resolve design flaws early. By creating a prototype, companies can test the functionality and usability of the product before mass production, reducing rework costs, which can be substantial when addressed during full-scale production. Moreover, with prototyping, companies can gather valuable feedback from potential customers and make necessary improvements based on their preferences.
By minimizing these expenses and incorporating customer feedback early on, companies can allocate resources to other essential aspects of their business, such as marketing and distribution. It saves costs and ensures the final product meets customer needs and demands.
As a result, companies can achieve increased profitability and gain a competitive edge.
Prototyping offers a cost-effective approach to product development by allowing companies to detect and rectify design flaws early on. By investing in prototyping, companies can optimize their resources, reduce rework costs, and ultimately increase profitability.
The future of prototyping
The manufacturing industry continues to evolve rapidly, with new technologies and processes constantly emerging. In this dynamic landscape, prototyping is set to revolutionize the industry by becoming an essential part of every manufacturing process.
With advancements in 3D printing technology, prototyping has become even more accessible and cost-effective. Companies can now easily create intricate prototypes, allowing for greater detail and functionality testing before mass production. This level of accuracy and efficiency has resulted in a surge of prototyping adoption across all industries, from automotive to healthcare.
Virtual prototyping, where digital models are created and tested through simulation software, is gaining traction in manufacturing. This innovative approach allows companies to develop prototypes without needing physical materials, further reducing costs and lead times while accurately representing the final product.
The last word
Prototyping has become an integral part of the manufacturing process, offering companies many benefits, from cost-effectiveness to fostering innovation. As technology advances, prototyping will become more accessible and powerful, providing manufacturers with a competitive edge in an increasingly fast-paced and demanding market.
Embracing prototyping is no longer an option but a necessity for manufacturing companies looking to remain competitive and deliver exceptional products that meet the needs of their customers. Manufacturers must integrate prototyping into their workflow, enabling them to stay ahead of the curve and achieve unprecedented success in today’s dynamic business landscape.