How Helpful Is thermo compression Bonding In Major Fields
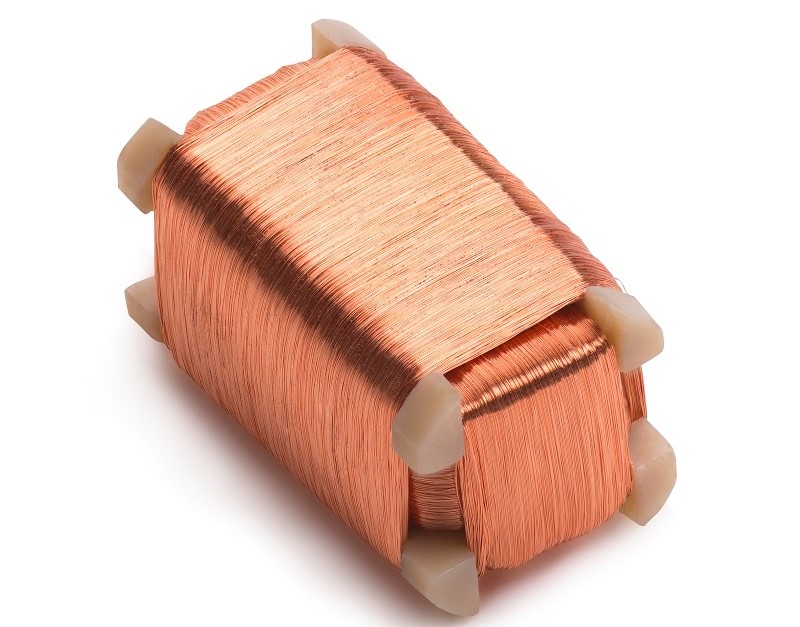
Due to its flexibility, thermo-compression bonding is employed in numerous industries. This is termed thermal compression welding or bonding. Heat and pressure create a strong connection between two materials. The precision and dependability of thermo-compression bonding in electronics, aerospace, medical devices, and car production make it successful. This discussion will analyse thermo-compression bonding’s advantages in these critical areas.
Benefits of Micro Compression Bonding
- Electronics
When assembling semiconductor devices and microelectronics, thermo-compression bonding is crucial. For connecting delicate electrical circuit components, this bonding procedure is ideal due to its precision and reliability. Some noteworthy electronics applications are:
- Wire Bonding
Small wires are bonded to semiconductor devices via thermo-compression bonding. Wires and semiconductors are securely connected by heat and pressure, which powers electrical equipment.
- Flipped Coin Bonding:
In flip-chip bonding, semiconductor chips are reversed and bonded to the substrate. Electrical connections between the chip and substrate commence thermo compression bonding. This approach provides high-density packing and better IC performance.
- COB device assembly
thermo compression bonding is essential for chip-on-board assembly, which involves directly mounting semiconductor chips to the substrate. This bonding keeps electrical connections intact, making electronic components used in consumer electronics, telecommunications, and computers reliable.
Aerospace
Aerospace component assembly requires reliability and precision. Hence, thermo compression bonding comes in play. Several key benefits of thermo compression bonding include:
- Microelectronics for aviation
In aircraft navigation, communication, and control systems, microelectronics are commonly used. Aircraft fly using these systems. thermo compression bonding ensures microelectronic component connection, improving avionic system performance and safety.
- Sensor data integration
Aircraft applications need sensors to monitor various aspects. Sensor integration onto circuitry uses thermo compression bonding, which ensures a reliable and long-lasting connection. This is essential for accurate data collection and system functioning in aeronautical applications.
- Spacecraft Component Bonding
In space, where temperature changes and mechanical stresses are high, thermo-compression bonding is a reliable method for joining spacecraft components. Stability from this bonding process improves crucial component durability and performance.
Surgical devices
The medical industry benefits from thermo-compression bonding for diagnostic equipment and device assembly. Due to its precision and cleanliness, bonding is ideal for applications that need hygiene and accuracy:
- Biochemical sensor integration
Medical equipment with biochemical sensors typically aids in diagnosis. These sensors may be securely incorporated into the device’s circuitry via thermo compression bonding, enabling accurate and reliable biological marker detection.
- Microfluidic Device Assembly includes:
Microfluidic devices for medical diagnosis and research use sophisticated channels and components. These devices are assembled using thermo compression bonding, which creates leak-proof, lasting connections that control fluid flow.
- Medical Implant Product Manufacturing
In pacemaker and neurostimulator production, thermo compression bonding secures electronic components. This bonding creates airtight seals, which make implanted medical equipment durable and safe.
Auto Manufacturing
thermo compression bonding is used in many automotive applications, improving performance, safety, and reliability. Examples of notable applications:
- Airbag deployment system
thermo compression bonding builds airbag deployment systems. This bonding method connects electrical components that release airbags quickly and correctly in a crash. These linkages must be reliable for passenger safety.
- Engine controller modules
Modern cars need engine control modules (ECMs) to manage engine functioning. By safely connecting semiconductor components within electronic control modules (ECMs), thermo compression bonding improves engine control system reliability.
- LED lighting systems
As LED lighting systems contact automobiles, thermo compression bonding is used to assemble and connect LED components. This bonding method extends the car lighting system life and increases visibility and safety.
Conclusion
Micro-compression bonding is a flexible bonding method with several benefits across sectors. Its accuracy, high bond strength, hermetic sealing, and material compatibility make it an essential technology in microelectronics and semiconductor manufacturing’s fast evolution. As technology advances, micro-compression bonding may shape smaller electronic devices and systems.