The most dangerous scam in aviation history? How mystery fraudster duped the world’s biggest airlines into using FAKE turbines, nuts and bolts in $3 MILLION scheme that had an army of hoax staffers and dummy offices including one near Buckingham Palace
A company accused of selling fake jet engine parts used in planes around the world was founded in Britain by a shady businessman who allegedly promoted the company with fake LinkedIn profiles and a ‘virtual’ office in near Buckingham Palace.
AOG Technics supplied parts used in at least 126 commercial aircraft engines in aircraft companies, including Delta and United.
But the parts were allegedly backed by forged paperwork and dozens of planes were grounded for urgent maintenance.
A lawsuit has now been filed in the UK against AOG Technics and it has emerged that the company has also engaged in a number of suspicious practices, including building a fake online presence to promote itself.
Parts were sold to other companies that airlines use for aircraft maintenance. They then turned them into commercial airplanes that could potentially carry millions of passengers.
LinkedIn profiles for employees who allegedly worked at AOG Technics contain stock photos that appear elsewhere on the Internet. One profile was for a man named Ray Kwong, who was listed as the company’s Chief Commercial Officer
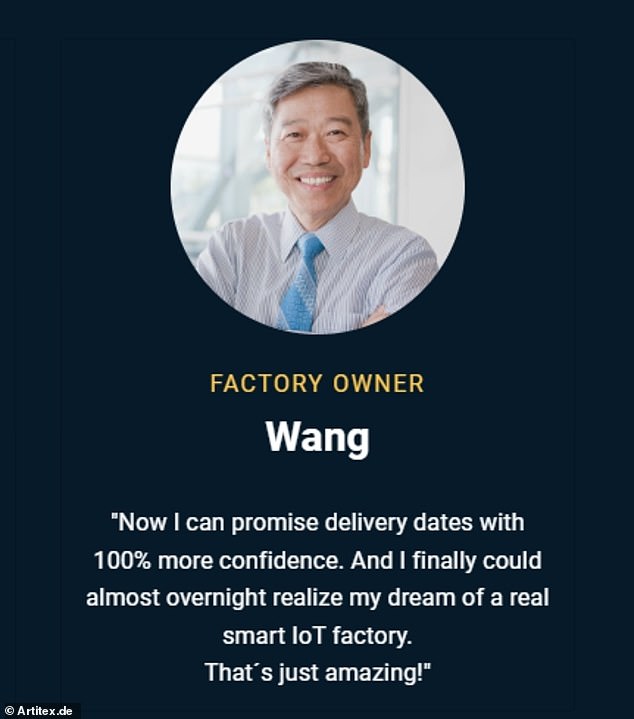
The image of Kwong is a stock photo that also appears elsewhere on the Internet, including on a textile website that lists the man as a “factory owner” named Wang
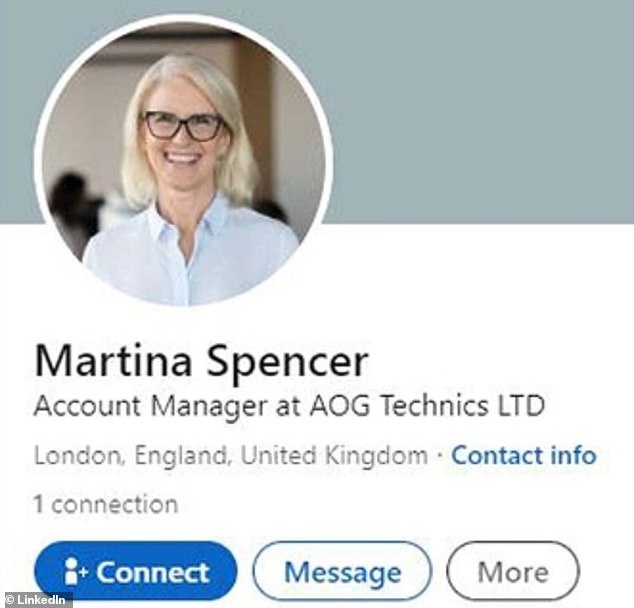
A LinkedIn profile of Martina Spencer, probably an account manager at AOG Technics, also appears to use a stock photo
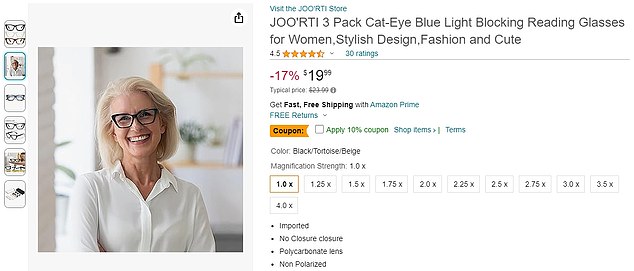
The image of Martina Spencer appears to be a stock photo of a woman who also appears in an Amazon listing for women’s reading glasses
The scandal raises serious questions about industry procedures designed to prevent unapproved parts from ending up on aircraft. The parts were used in CFM56 engines, the world’s best-selling jet engine, used in aircraft including Airbus A320 models and the Boeing 737.
AOG Technics was founded in Britain in 2015 by Jose Alejandro Zamora Yrala, believed to be a 35-year-old man from Venezuela. He has not commented on the scandal.
LinkedIn profiles for employees who allegedly worked at AOG Technics contain stock photos that appear elsewhere on the Internet, including in promotional materials for other companies. Many of the LinkedIn accounts have now been deleted.
One profile was for a man named Ray Kwong, who was listed as the company’s Chief Commercial Officer. Kwong mentioned previous experiences at Mitsubishi and Nissan, but neither has been able to confirm he was employed by them.
His photo shows a gray-haired man in a neat shirt with a striped blue tie. The same image also appears on other web pages, including that of a textile company that claims the man is a “factory owner” named Wang.
Another employee was listed on LinkedIn as Martina Spencer, believed to be an account manager for AOG Technics. Her photo appears to be another stock photo of a woman whose image was also used in an Amazon listing for women’s reading glasses.
The company also boosted its image by using a ‘virtual’ office in central London, just a few minutes’ walk from Buckingham Palace.
Anyone who searches the address – the Nova Building at 79a Buckingham Palace Road – will find a luxury office building with a glass facade.
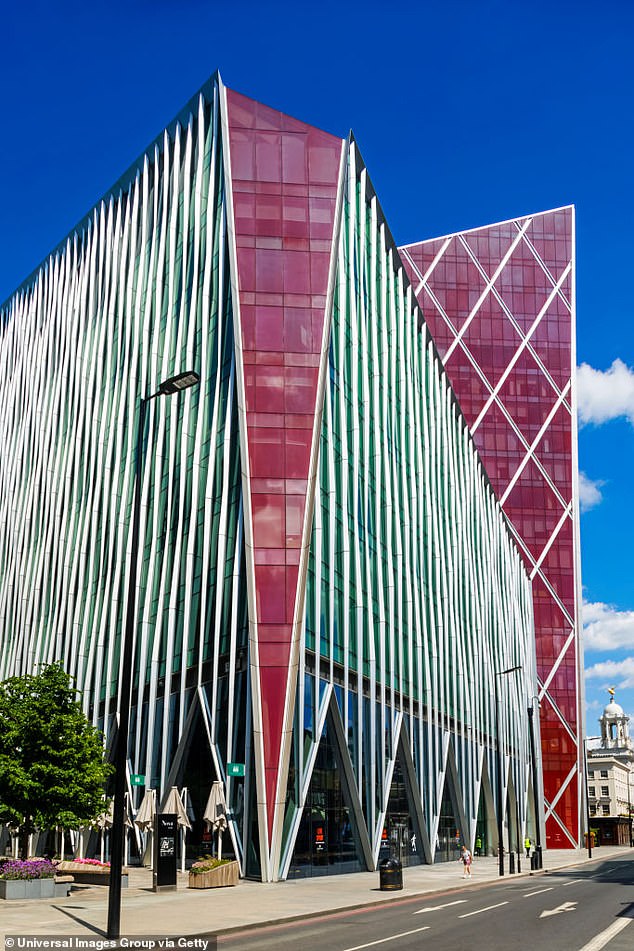
The company also boosted its image by using a ‘virtual’ office in central London, just a few minutes’ walk from Buckingham Palace. In reality, AOG Technics has no physical presence there at all and appears to have simply rented a mailing address for just $150 per month.
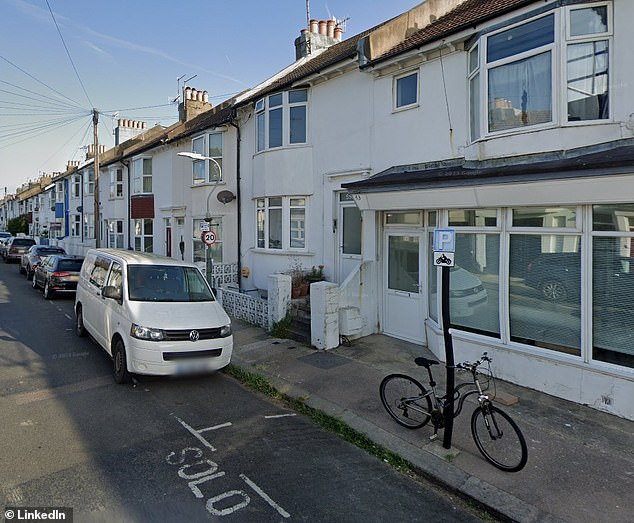
Documents show the company was founded in 2015 and was initially listed at a residential address in the seaside town of Hove, in southern England.
In reality, AOG Technics does not have a physical presence there at all. The company appears to have simply rented a mailing address for just $150 per month.
Business records in Britain show that the company’s first official address was a small house in the seaside town of Hove, in southern England. It then occupied a second residential building in Hove before moving to London in 2017, eventually settling in The Nova Building.
Documents signed by Yrala also show that the company had approximately $3 million in assets as of 2022, indicating the size of the business.
Aviation experts have wondered how an alleged fraud of such scale could occur in an industry fraught with regulation – and where one faulty part could potentially cost the lives of hundreds of people.
Phil Seymour, chief executive of UK aviation consultancy IBA, said: ‘This is not a new problem in the sector. There have always been people who wanted to make money with aircraft parts.
‘The big problem here is that these parts have found their way into engines; that is the game-changer for me.’
CFM, the company whose engines were affected by the scandal, said there have been no reports of the use of counterfeit parts. Instead, the problem centers on thousands of parts with suspected fake documentation. Some have gone unnoticed for years.
It is not clear how AOG Technics obtained the parts.
CFM fears that false paperwork could be used to pass off old parts as new or to offload parts that do not have the traceability needed to ensure they are safe.
In one case, paperwork on the sale of a key component, a low-pressure turbine, to a Florida company in 2019 was signed by a man named “Geoffrey Chirac,” who is believed to be a non-existent employee of AOG Technics.
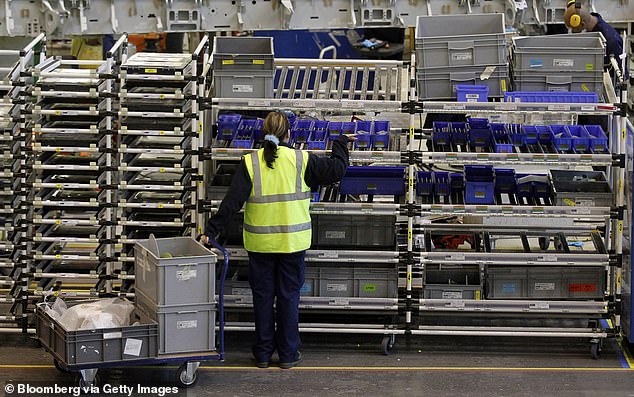
The scandal has rocked the aviation industry, with parts ranging from small nuts and bolts to all-important turbine blades potentially failing. Pictured: production of parts for an Airbus A320 wing
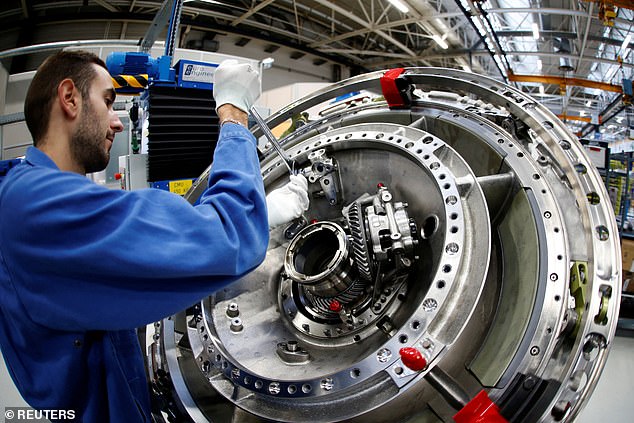
The most affected engine model appeared to be a CFM56 (pictured), which, at over 33,900, alarmingly holds the record for the most engines ever sold to airlines.
According to CFM court documents, the alarm was first raised on June 21 when TAP Air Portugal’s maintenance department said it had concerns about documentation for a small part called a damper that it had obtained from British distributor AOG Technics.
“The part appeared to be older than depicted,” CFM said.
The birth certificate that must accompany each aerospace unit contained a forged signature, according to a newly released court filing detailing the extent of the detective operation.
According to CFM, within 20 days the same airline had found 24 forms from the same vendor with ‘significant differences’.
AOG told a British court last month that it was “fully cooperating” with investigations without commenting on CFM’s claims.
Although developers of aircraft parts are strictly regulated and require separate approval to produce them, no formal permission is required to set up warehouses to distribute them.
“That’s an area of regulation that needs to be looked at because most retailers self-certify,” Seymour said.
“They realize it’s not in their interest to supply counterfeit parts, so they have their own quality systems and a lot of self-regulation, but no official regulatory approval.”
The alleged fraud is yet another scandal to rock the airline industry, including controversies in the US over near misses and flight cancellations.
Recent examples include several cases of planes nearly colliding with each other while taking off or landing at major U.S. airports. Others include a near-miss in mid-air between two planes traveling at more than 500 miles per hour.
They are among the 46 ‘close calls’ in July. Industry workers blame a shortage of air traffic controllers, forcing many in the profession to work mandatory overtime. The demands of the job have left some burned out and even turning to alcohol and sleeping pills to relieve stress.
A shocking 99 percent of U.S. air traffic control facilities are understaffed, according to U.S. Air Traffic Control New York Timeswhich showed that 310 out of 313 do not have enough employees.
Some, including the regional office in New York and a tower in Philadelphia, are operating at about 60 percent of staff or less.